The development of Cosmetic Filling
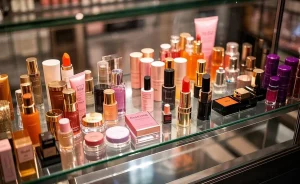
Cosmetics play a significant role in the female consumer market. They have always been a popular area for spending. As society develops and living standards improve, women’s demand for cosmetics goes beyond basic skin care and makeup. They focus more on product quality. They also consider packaging design and usage experience. This trend has caused the cosmetics market to expand continuously. The demand keeps rising, bringing significant benefits to the cosmetics filling industry.
The innovation and progress of cosmetic filling technology is very important. This context highlights its significance. Efficient filling equipment meets the needs of large-scale production. It also ensures stability and consistency in the quality of each product. Automated filling lines cut down on manual operation errors. They enhance production efficiency and lower costs. The demand for personalized and eco-friendly packaging is rising. As a result, the cosmetics filling industry is innovating. They are launching more packaging solutions that align with market trends.
The cosmetics filling market is experiencing significant growth. It has become a key area for many companies to compete and establish their presence. High-end luxury brands and mass daily chemical brands are both seeking cooperation. They want to partner with leading companies in filling technology. This is essential to stand out in fierce market competition. Cosmetics filling is a technology-intensive industry. It is also a field rich in creativity and innovation. It has great development prospects. There is huge potential.
What is the cosmetic filling machine?
A cosmetics filling machine is a device. It is used to fill cosmetic products into packaging containers. The cosmetics filling machine works by accurately filling products into packaging containers. This is accomplished by controlling the feeding valve’s opening and closing. Its workflow usually includes steps such as preparation, feeding valve control, filling container positioning, filling start, filling stop, and restart, realizing an automated filling process. Its working principle mainly involves the following steps:
- Preparation
The operator places the cosmetics to be filled in the feeding device of the machine and prepares empty packaging containers, such as bottles or tubes and places them in the filling position. - Feeding valve control
The feeding valve of the machine automatically opens and closes according to the set filling volume. When the valve is opened, the cosmetics will flow from the feeding device into the valve. - Filling container positioning
The machine accurately places the container to be filled at the filling position through the positioning device. This is usually achieved by adjusting the sensors and positioning devices on the machine. - Filling starts
After the container is in the filling position, the machine starts the main motor to control the opening and closing of the feeding valve. When the valve is opened, the cosmetics will enter the container.
The types and characteristics of cosmetic filling machine
Type
Cosmetic filling machines come in two main types. These are semi-automatic and fully automatic machines. Semi-automatic filling machines need some manual tasks. This includes placing containers and adjusting the filling volume. Fully automatic filling machines can complete the entire process automatically. This includes container transportation, filling, sealing, and packaging.
Additionally, cosmetic filling machines can be categorized based on the filling materials. They include paste filling machines and liquid filling machines, among others. Paste filling machines work well for viscous paste materials. This includes face creams and eye creams. Liquid filling machines are designed for liquid materials. Examples are lotions and essences.
Characteristics
- High precision: Cosmetic filling machines often utilize high-precision metering pumps. They may also use electronic weighing technology. This ensures that the filling volume of each product is consistent and accurate. It meets the requirements of cosmetic companies for filling accuracy.
- High degree of automation. Modern cosmetic filling machines have automated control systems. These systems can significantly reduce manual intervention. They also improve production efficiency. Fully automatic filling machines can work with conveyor belts. They also connect with packaging equipment. This setup achieves streamlined production from filling to packaging.
- Strong applicability. Cosmetic filling machines can adapt to materials with different viscosities. They can also handle containers of various specifications. Adjusting the filling head and conveying system makes it easy to meet the filling needs of different cosmetics.
- Easy operation: The cosmetic filling machine has a smart design. It is simple to use. A semi-automatic filling machine needs just one operator. This can significantly lower labor costs.
- Hygiene and safety: Cosmetic filling machines are typically made of stainless steel. They also meet hygiene standards. The filling system features an anti-drip design. This helps prevent contamination from liquid overflow during production.
The Application and Advantages of Cosmetic Filling Machine
Cosmetic filling machines are used in various applications. They are primarily found in the cosmetics industry. This includes products like skin care water, lotion, essence, perfume, and shampoo. They handle both fluid and semi-fluid products. These products require high standards. They need precise appearance accuracy. Equipment stability is also crucial. Additionally, filling accuracy must be maintained.
Cosmetic filling machines offer several advantages. These benefits are evident in various aspects.
- Precision filling: Modern cosmetic filling machines use high-precision flow meters. They also utilize electronic weighing technology. This ensures that each bottle’s filling volume meets the set value. It helps avoid waste or insufficient filling. This high-precision filling capacity is ideal for the cosmetics industry. It meets strict dosage requirements.
- High degree of automation. The equipment features an automated control system. It includes functions like filling volume setting, bottle identification, and liquid flow rate adjustment. This setup reduces manual intervention and significantly boosts production efficiency. The linkage operation with the conveyor belt and packaging equipment enables streamlined production. This process runs smoothly from filling to packaging.
- Strong adaptability: The cosmetic filling machine can manage liquids with varying viscosities. It works well with everything from liquid lotion to thick cream. The filling head and conveying system are adjustable. They can adapt to different bottle types and capacities. This flexibility meets the needs of cosmetic companies for product diversification.
- Hygiene and safety. The equipment is made of stainless steel. It meets the hygiene standards of the cosmetics industry. The filling system has a drip-proof design. This helps avoid contamination from liquid overflow during production. It ensures the product’s hygiene and safety.
In summary, cosmetic filling machines are crucial in the cosmetics industry. They offer precise filling and high automation. Their strong adaptability and hygienic safety are also significant. These machines provide efficient and stable solutions for cosmetics production.
The Maintenance of Cosmetic Filling Machine
Maintaining and caring for cosmetic filling machines is essential. This ensures normal operation and extends their service life. Here are key maintenance steps. Also, some care tips:
- Clean daily.
After each use of the cosmetic filling machine, clean the connecting pipes promptly. This is especially important when changing products. Use clean water to flush the pipes three times. This ensures that there is no residue left in the pipes. Wipe the dust and any residual liquid from the machine’s surface. Use a semi-dry towel to prevent corrosion. Also, wipe the buttons and connecting lines on the control panel. Use a dry towel to keep them clean and dry. - Inspect regularly. Replace as needed.
- Check the air intake filter once a month. Also, inspect the exhaust filter. Make sure they are not blocked or damaged.
- Replace the vacuum pump oil and oil filter every 500 to 2000 hours. Check the oil level and color. If the oil level is below the MIN mark, add oil. If it exceeds the MAX mark, drain some oil. The vacuum pump oil should be bright and clear. It must not have any foam or turbidity. If needed, replace with new oil.
- Clean the dust and dirt in the vacuum pump cavity every six months. Also, clean the fan engine cover, fan wheel, ventilation grille, and cooling fins.
- Replace the exhaust filter annually. Clean or replace the intake filter as needed.
Professional maintenance Care in the Cosmetic Filling Machine
- The switching speed of the filling valve can be adjusted. This can be done by changing the spring pressure of the valve. A higher viscosity in the material results in a slower speed for the filling valve switching. Increasing the spring pressure will boost the switching speed of the filling valve.
- Lubricate the gear meshing points regularly. Also, oil the spray holes and moving parts of the filling machine. This will help keep everything in good operating condition.
- Regularly check the connection lines and connectors of the filling machine. This helps prevent loose connectors from affecting filling accuracy. It also avoids safety accidents like leakage and short circuits.
- Professional operators must be skilled in startup and bag making procedures. They should also handle simple instrument debugging and parameter changes. This ensures the machine operates normally.
- Troubleshooting
If the cosmetic filling machine fails, it may not work properly. Materials cannot be filled normally. In this case, turn off the power immediately. Check the circuit, fuse, switch power indicator, and other components. Replace any damaged parts promptly. At the same time, check if the touch screen is connected properly. Also, verify the PLC communication line of the equipment. This ensures normal communication of the equipment.
The cosmetic filling machine needs regular inspection and maintenance by professionals. The operator should also learn some maintenance and care knowledge. This ensures the machine operates normally and extends its service life.